The “DC” Dyno Cell
This test cell is named for the electric motor type used by the dynamometer in the cell. It not only provides absorption of the engine’s power, but also allows the ability to ‘motor,’ or drive, the same engine for nearly endless testing possibilities.
The cell’s data acquisition system features a full combustion analysis system, in-cylinder pressure sensors, a laminar flow element, a fuel flow meter, and various pressure and temperature sensors monitoring all aspects of the test engine’s inputs and outputs.
Engine control is most often the duty of a dSPACE system, but other systems are also used to meet customer needs.
The "DC" Dyno Control
The operation of the DC test cell is controlled via multiple screens and multiple PCs. This allows for real time monitoring of the engine’s parameters as well as recording all inputs and outputs for detailed analysis by the engineers.
The “EC” Dyno Cell
The EC test cell features an eddy current dynamometer, which absorbs power from the test engine.
This cell’s data acquisition system also features a full combustion analysis capability, in-cylinder pressure sensors, a laminar flow element, a fuel flow meter, and various pressure and temperature sensors monitoring all aspects of the test engine’s inputs and outputs.
Engine control is most often the duty of a dSPACE system, but other systems are also used to meet customer needs.
The "EC" Dyno Control
The operation of the EC test cell is controlled via multiple screens, multiple PCs as well as a control console. This allows for both real time monitoring of the engine's operating parameters as well as logging all inputs and outputs for subsequent detailed analysis.
The Chassis Dyno
The chassis dynamometer also utilizes the power absorption capability of the eddy current design. It is used to run emissions tests comparisons, to verify functionality of our latest vehicle builds, and to reverse engineer OEM calibrations.
Emissions Testing
The trio of dyno's all have the ability to connect to a pair of Horiba Mexa One Emission Analyzers as well as a TSI Engine Exhaust Particle Sizer for measuring both Particulate Number and Mass.
The Fabrication Area
This area has all of the essentials needed for the build out of the dyno test cells, engines, test equipment and vehicles.
Electrical Engineering Laboratory
The EE lab simultaneously hosts a variety of processes. It has dedicated work spaces for printed circuit board layout, wire harness design and prototyping, as well as the design and manufacturing of the one-off components needed to integrate many other devices in the dynos and vehicles.
Simulation
Another important activity happening in the EE Lab area is the control system simulation on the Hardware In the Loop (HIL) bench. HIL ensures that software and simulation work can be verified while running actual hardware components.
Electric Motor Technology
The final stop on the tour of the EE lab is the electrical motor dyno. This test set-up features inverters designed and built in-house by the Tula team and allows us to test some of our upcoming Dynamic Motor Drive, or DMD, concepts.
Interested in joining the team?
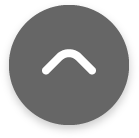