Dynamic Skip Fire
DSF® technology delivers 5-15% efficiency gains in passenger vehicles
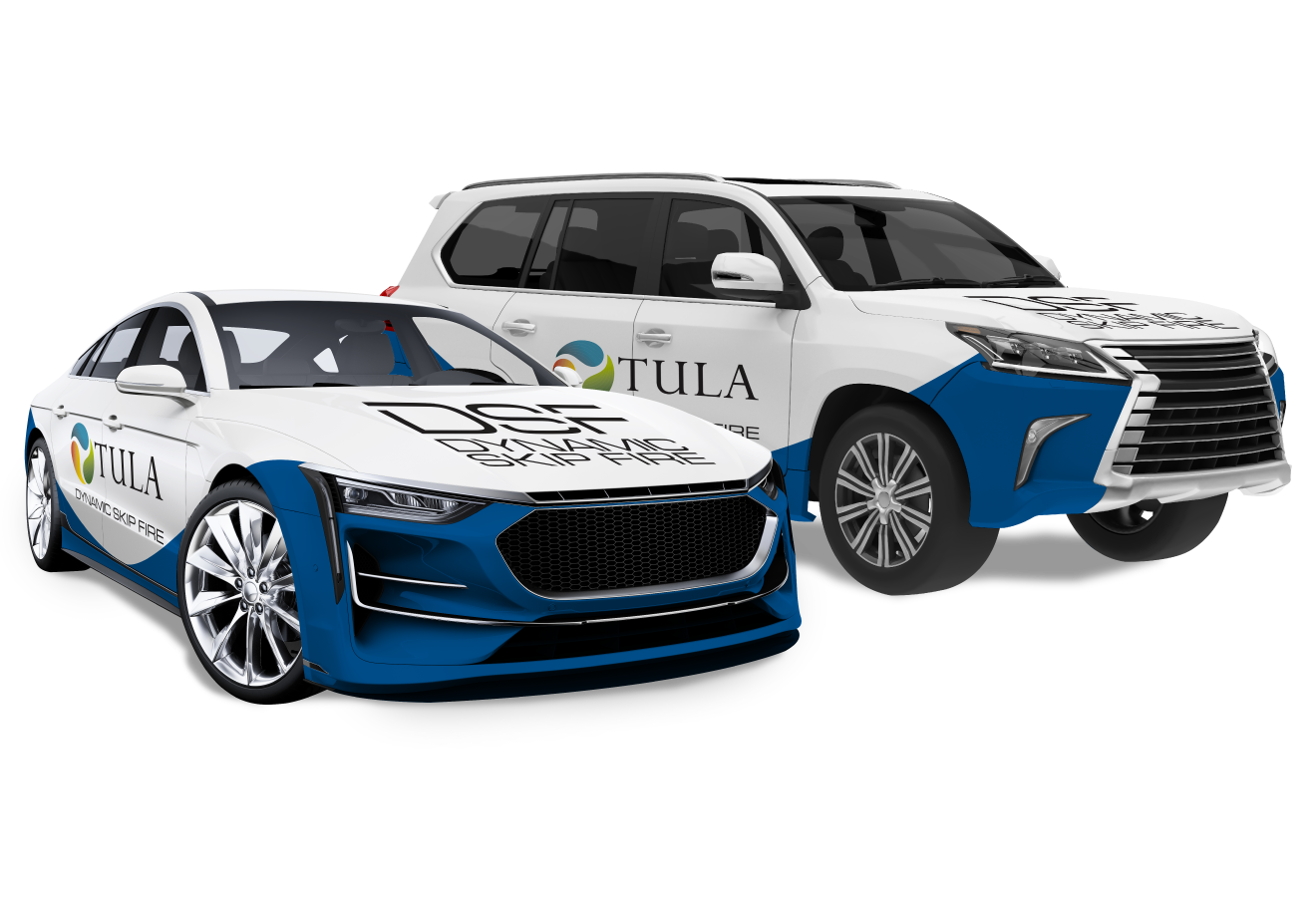
How Dynamic Skip Fire (DSF®) works
DSF skips or fires individual cylinders dynamically on an event-by-event basis to meet the requested torque from an engine. Through careful control of the number and sequence of combustion events using patented algorithms, engine operation occurs near peak efficiency, creating a software-controlled variable displacement engine. Tula’s algorithms avoid noise and vibration generation to give drivers expected levels of refinement under all driving conditions.
DSF® in real world situations
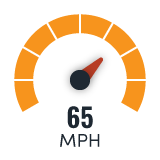
When high torque is needed, DSF® activates all cylinders.
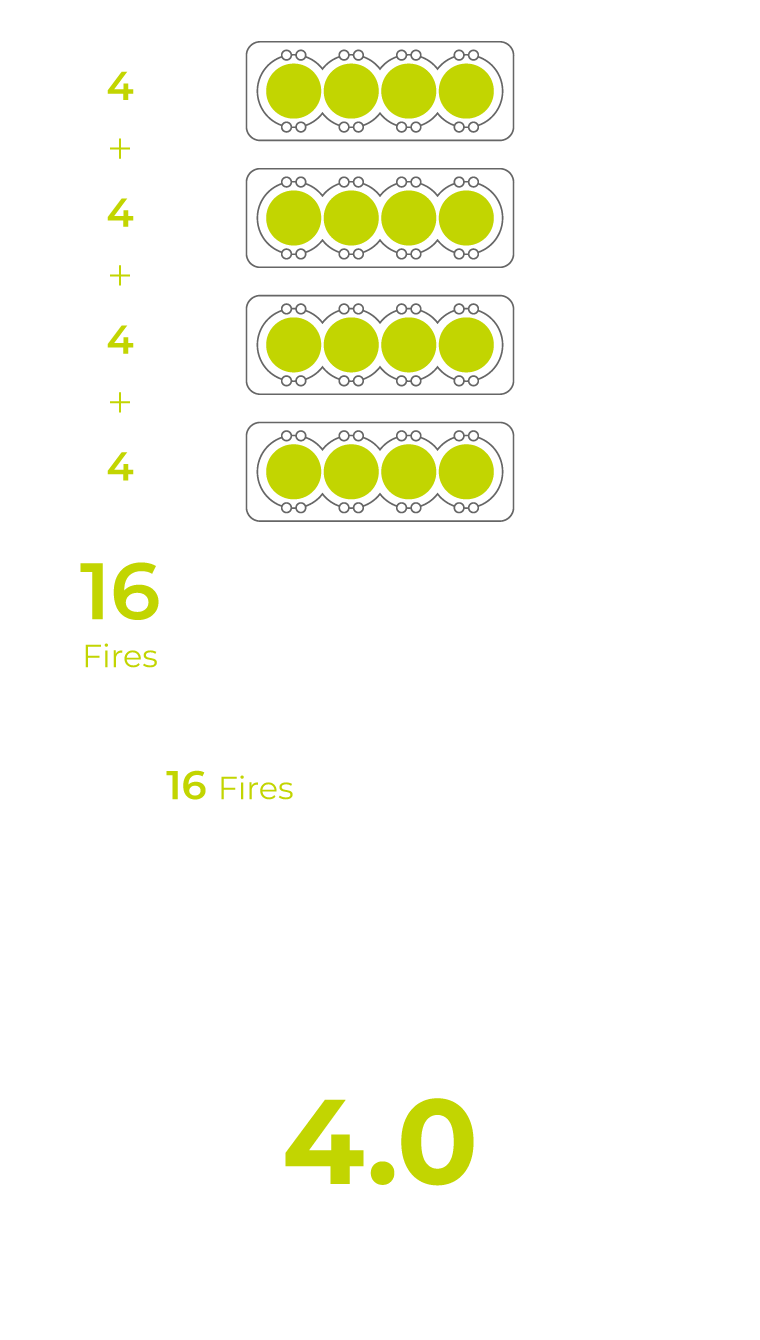
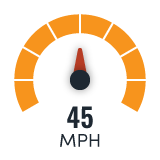
As torque demand moderates, cylinders are dynamically skipped based on demand.
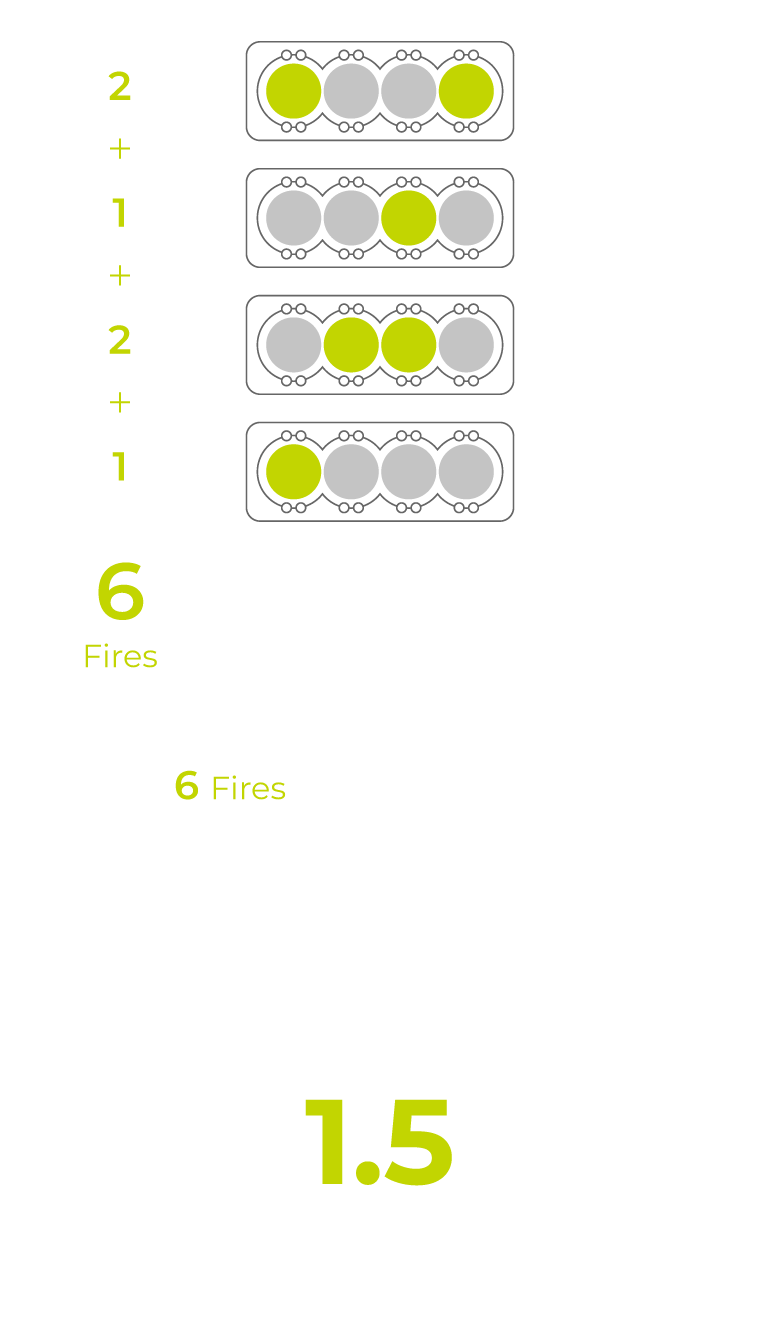
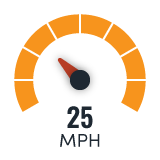
At slower speeds, maximum fuel efficiency is maintained by skipping more cylinders, even skipping all cylinders during deceleration.
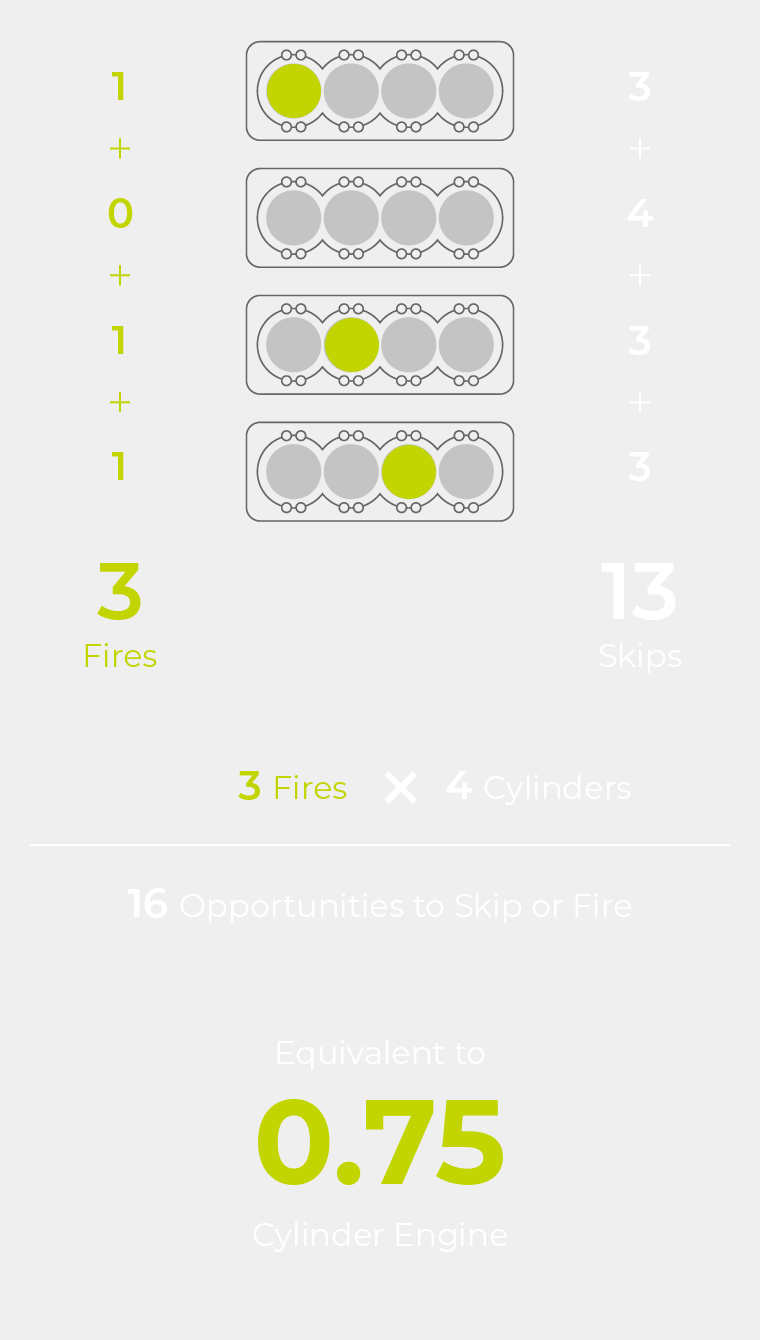
How DSF is implemented
Software in Engine Control Module
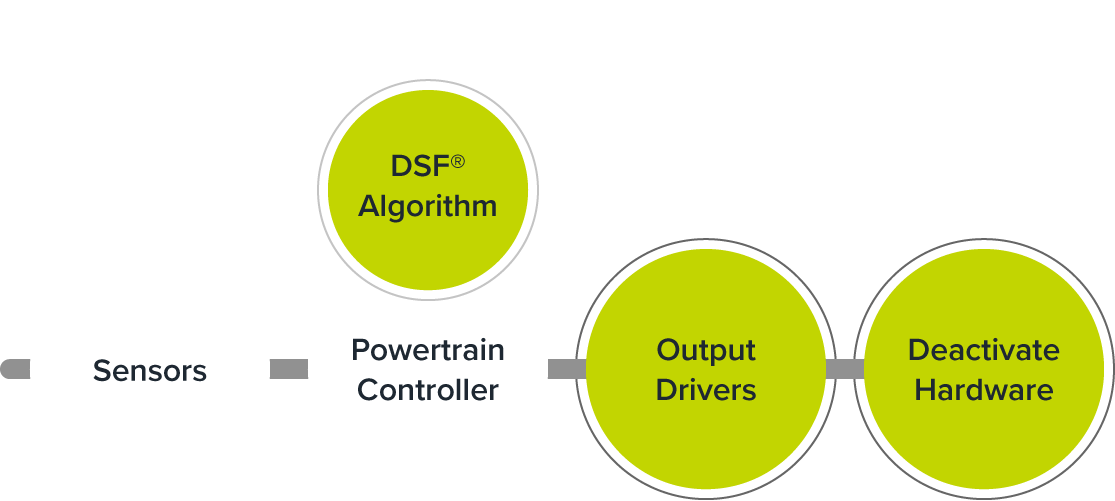
Cylinder Deactivation Hardware
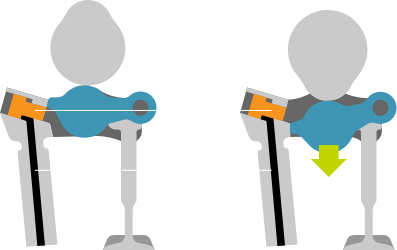
Tula’s DSF works with most deactivation valvetrains
DSF relies on individual cylinder deactivation. Each cylinder fire or skip needs to be controlled by deactivation capable intake and exhaust valves.
Valve deactivation can be through hydraulic or electromechanical means.
DSF has an excellent value proposition as evidenced by more than two million vehicles with DSF on the road today
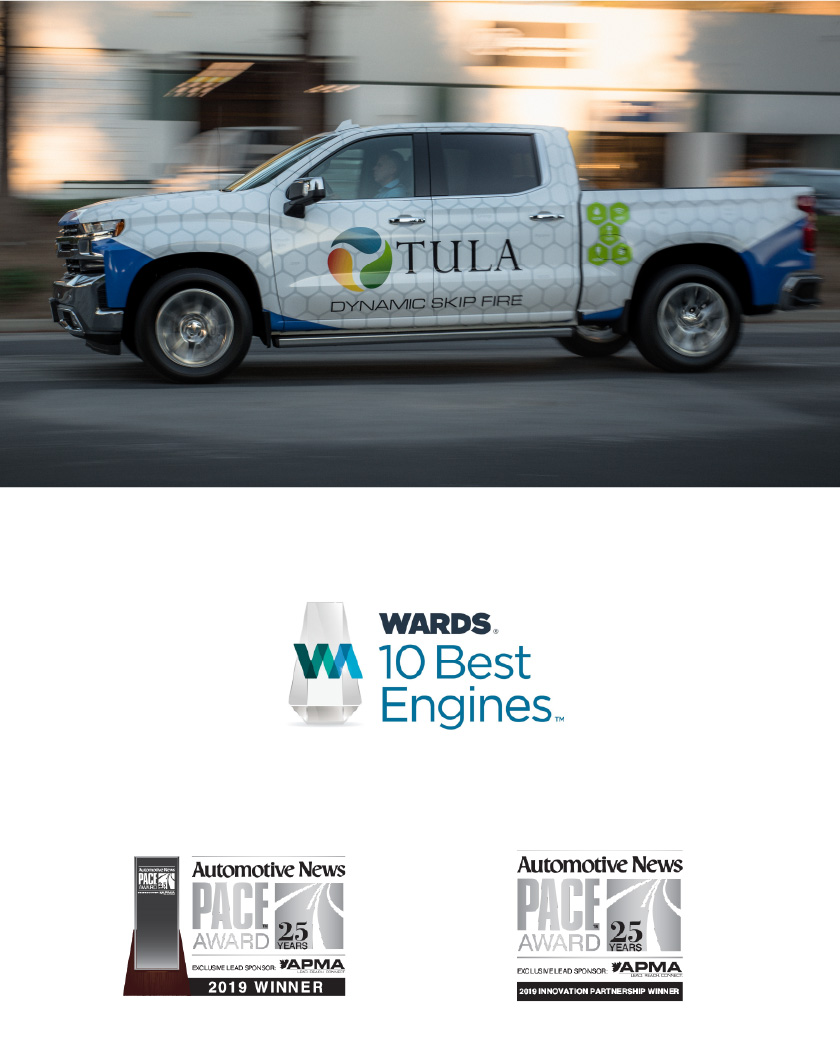
Tula has developed one of the “essential technologies
for reaching fuel efficiency mandates”
Click to learn more about Tula and our dedication to a cleaner Earth
Diesel Dynamic Skip Fire
Dynamic Skip Fire for Diesel Engines (dDSF™) enables diesel engines to be both clean and green
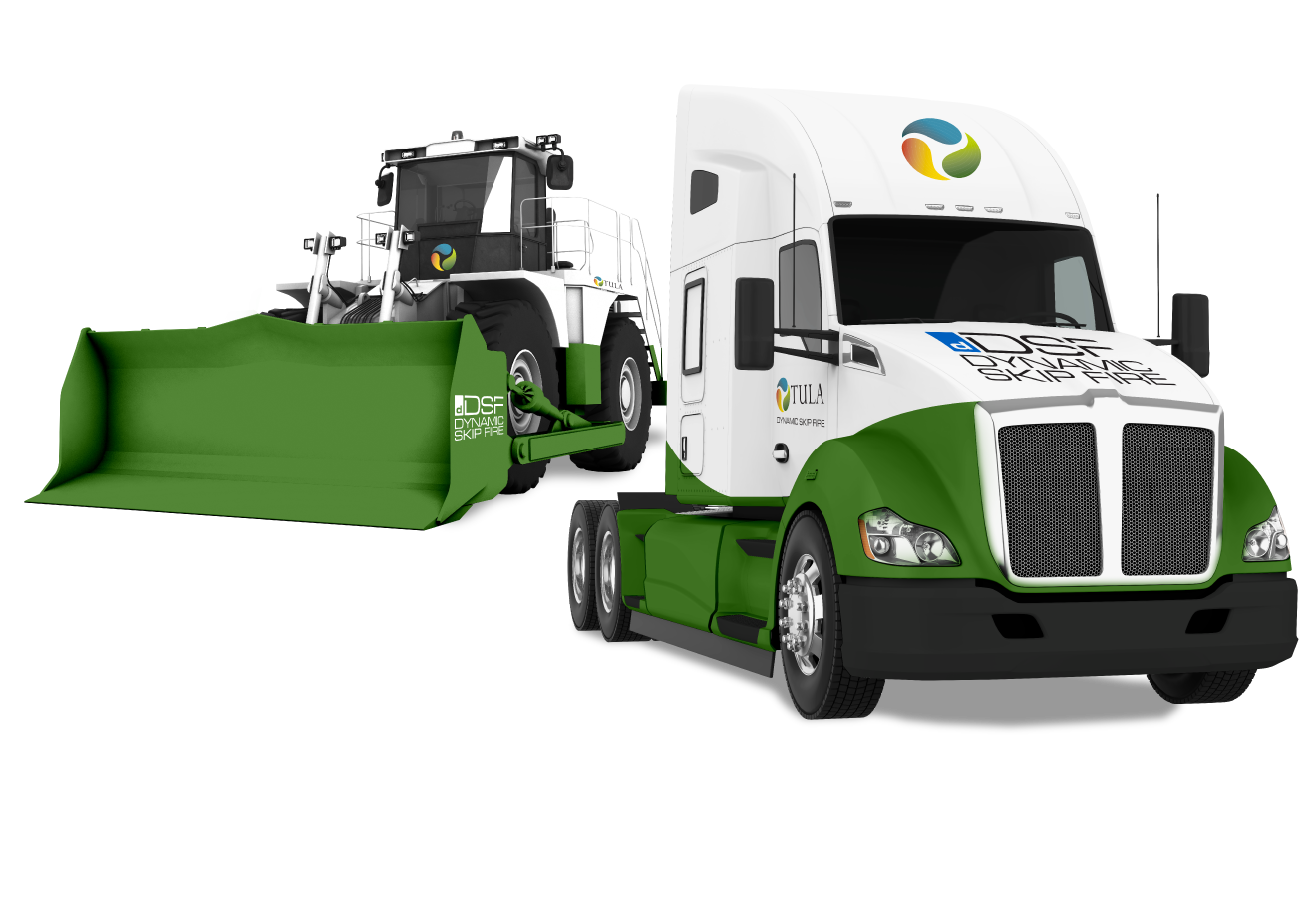
How Diesel Dynamic Skip Fire (dDSF™) works
Tula’s dDSF technology carefully controls the number and sequence of combustion events in a diesel engine using patented algorithms to ensure the engine operates near peak efficiency. Due to the higher cylinder load, dDSF also increases exhaust gas temperatures to continue keeping the aftertreatment system at operating temperature, especially under low-load conditions.
dDSF™ in real world situations
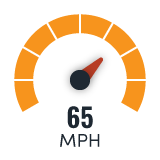
When high torque is needed, dDSFTM activates all cylinders.
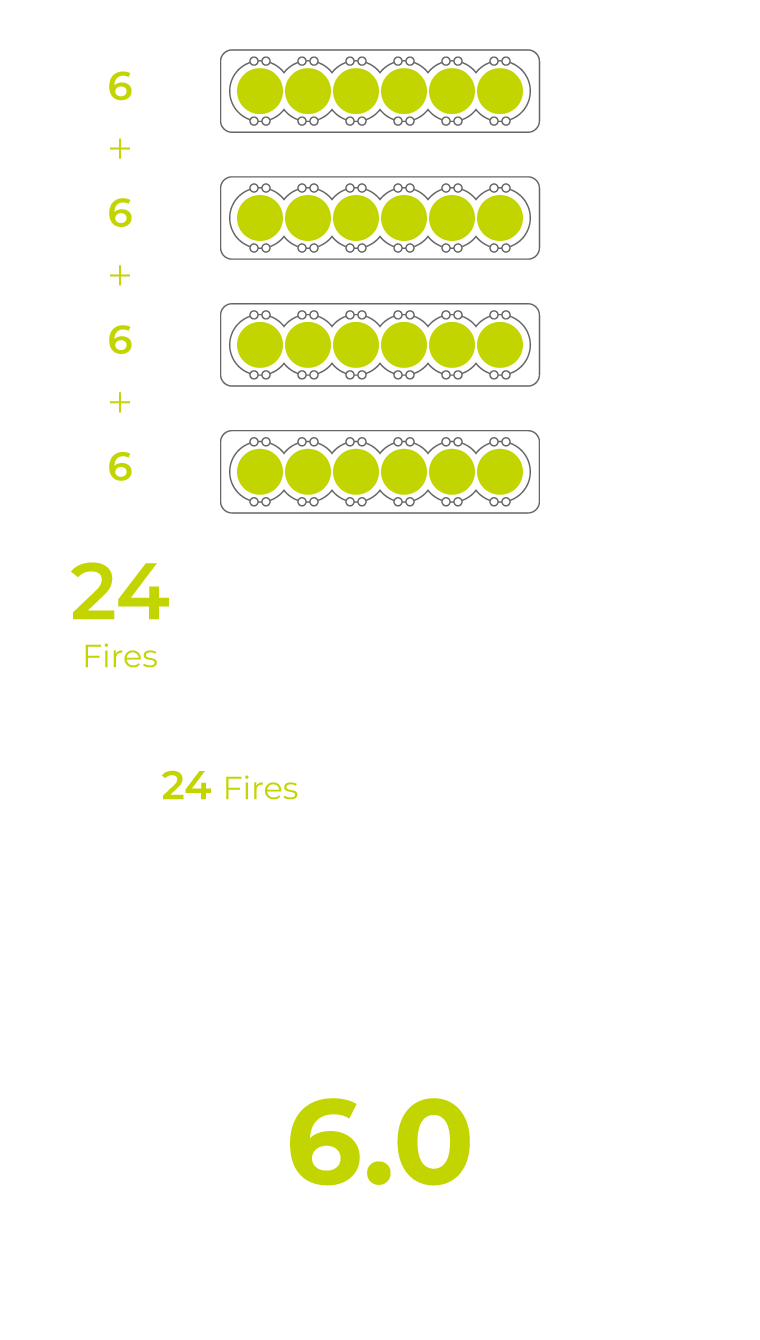
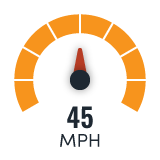
As torque demand moderates, cylinders are dynamically skipped based on demand.
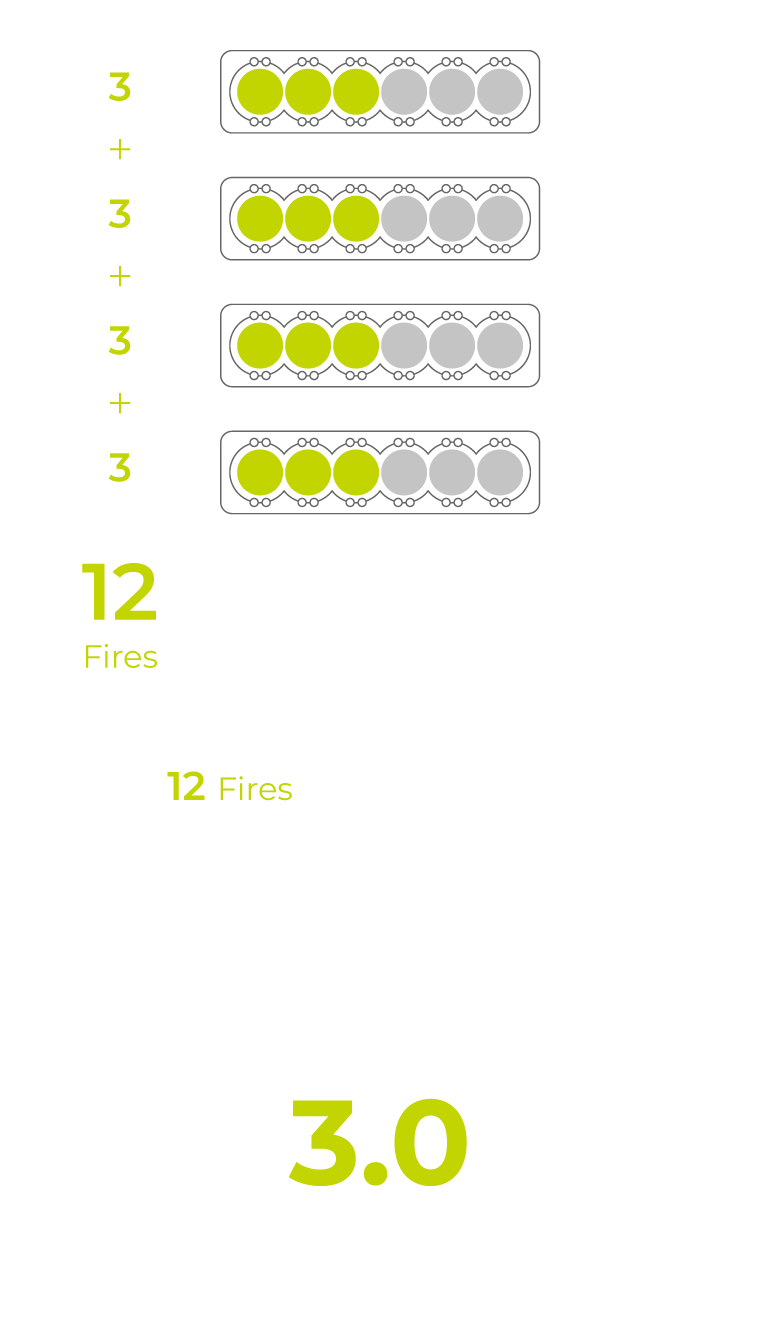
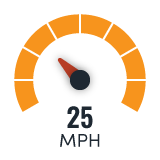
At slower speeds, maximum fuel efficiency is maintained by skipping more cylinders, even skipping all cylinders during deceleration.
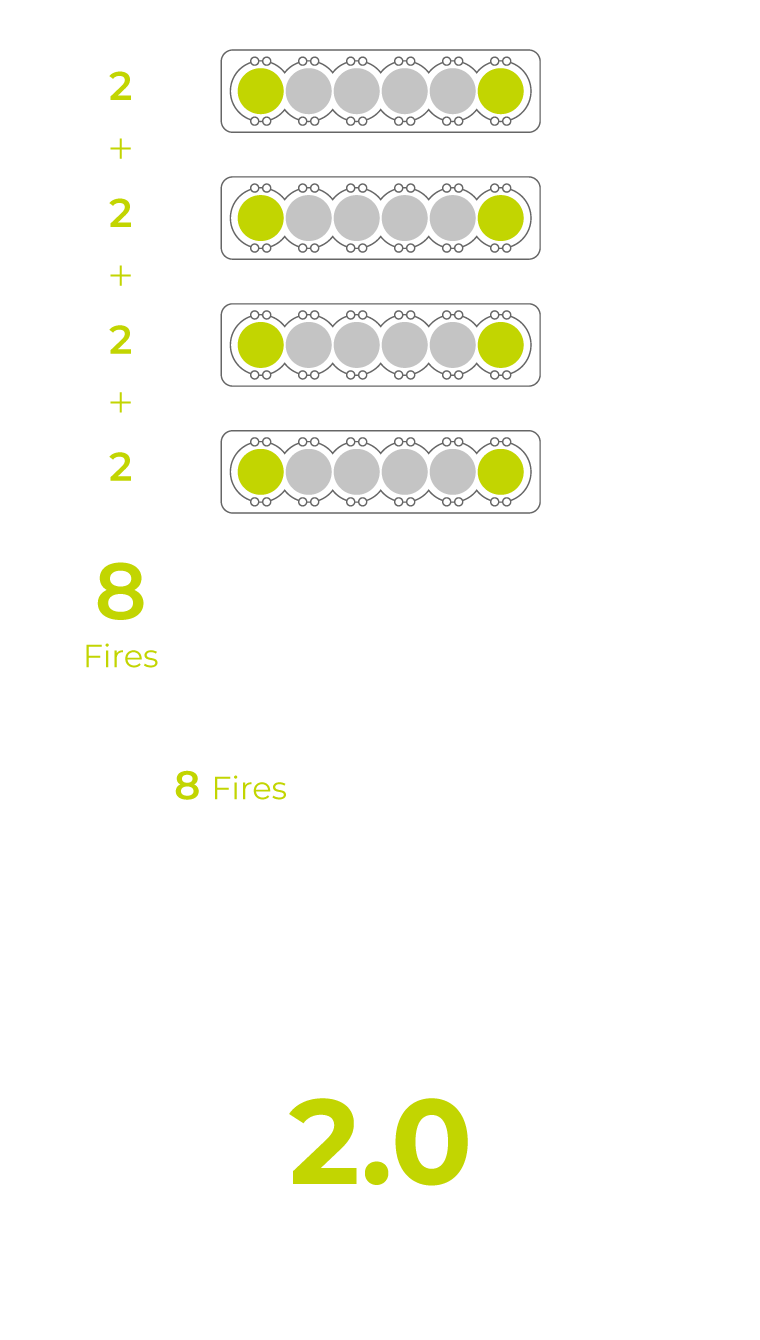
Simultaneous CO2 and NOx benefits from optimal combustion
and greater conversion efficiency
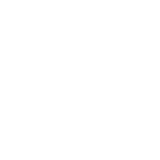
Engine Controls
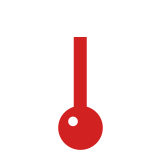
Temperatures
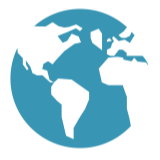
and NOx Reduction
Optimal Combustion
Reduced CO2
dDSF improves fuel efficiency by firing all events at the most efficient air to fuel ratio, allowing optimal combustion at all engine output levels.
Conversion Efficiency
Reduced NOX
Cylinder deactivation reduces excess engine airflow and increases exhaust temperatures. This allows for more efficient conversion of pollutants in the catalyst and reduced NOx - at the same aftertreatment system cost.
Test results show 74% NOx and 5% CO2 reduction
Results shown are mapped for appropriate firing densities. The improvement in turbine outlet temperature is dramatic, allowing effective aftertreament control.

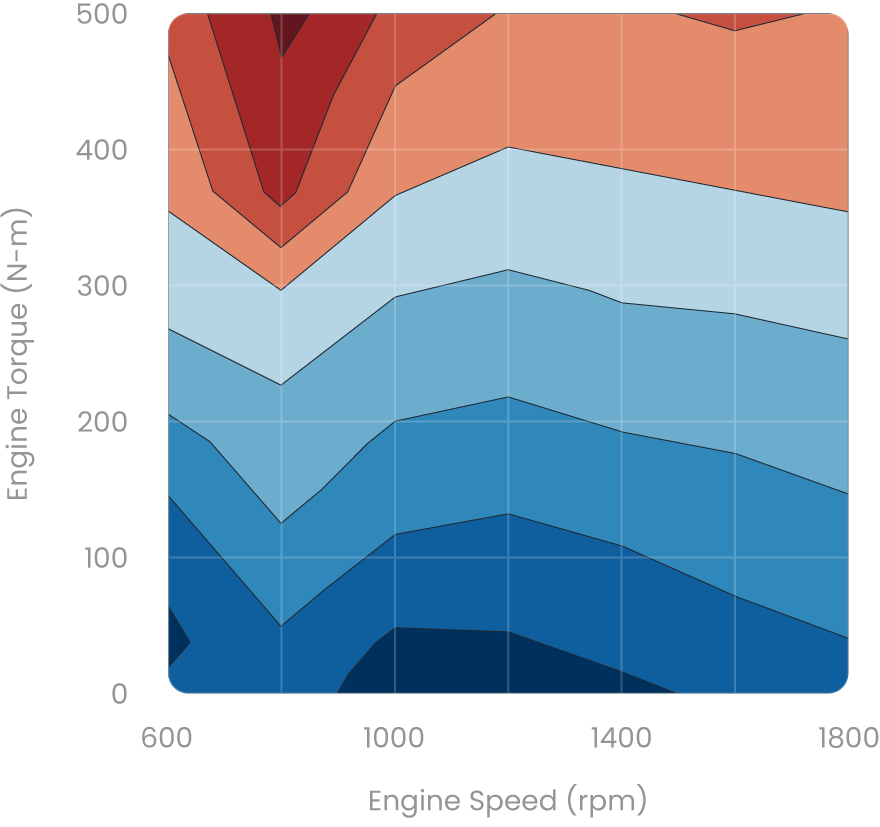
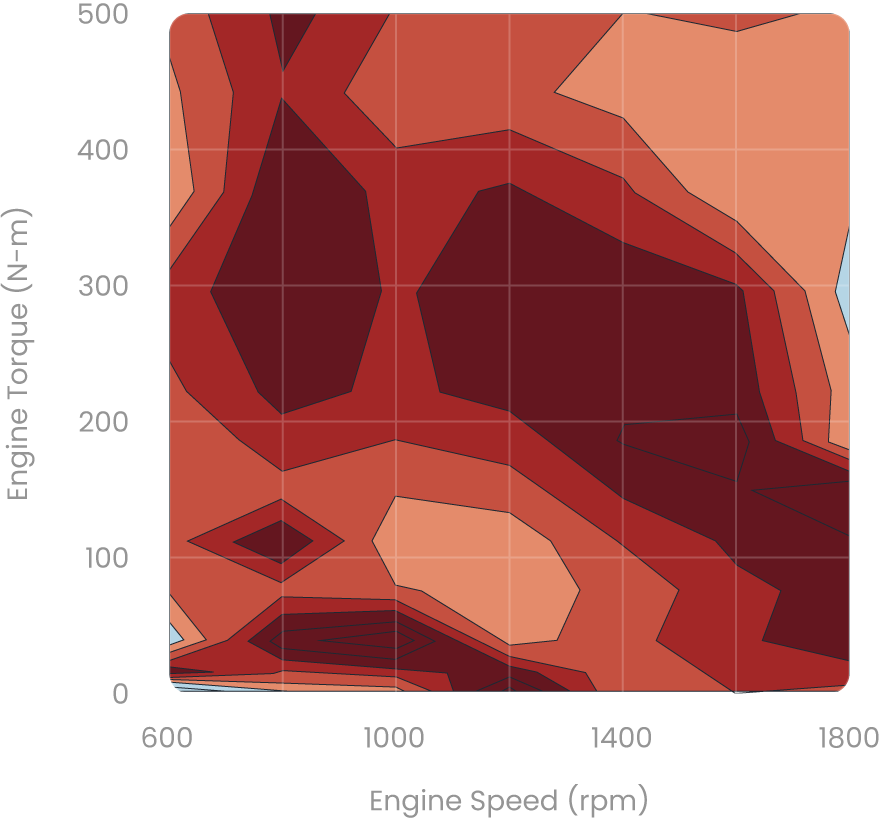
Valve Train Deactivation Mechanizations for Diesel Engines
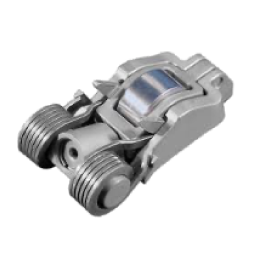
Deactivation
Finger Follower
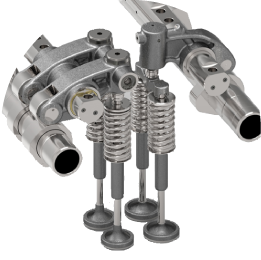
Deactivation
Rocker Arm
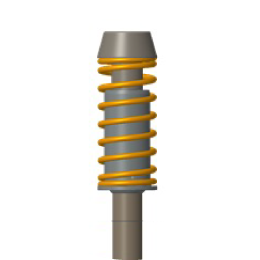
Deactivation
Pushrod Cartridge
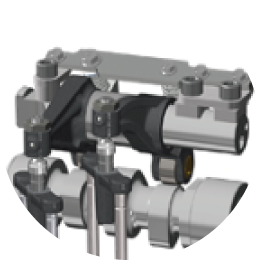
Deactivation
Valve Bridge
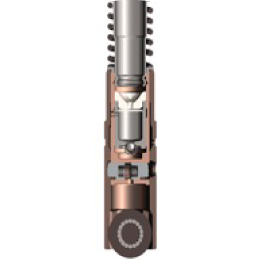
Deactivation
Roller Lifter
Global regulations are becoming increasingly stringent for heavy-duty diesel NOX and CO2 emissions. dDSF simultaneously reduces NOX and CO2 emissions at a low cost.
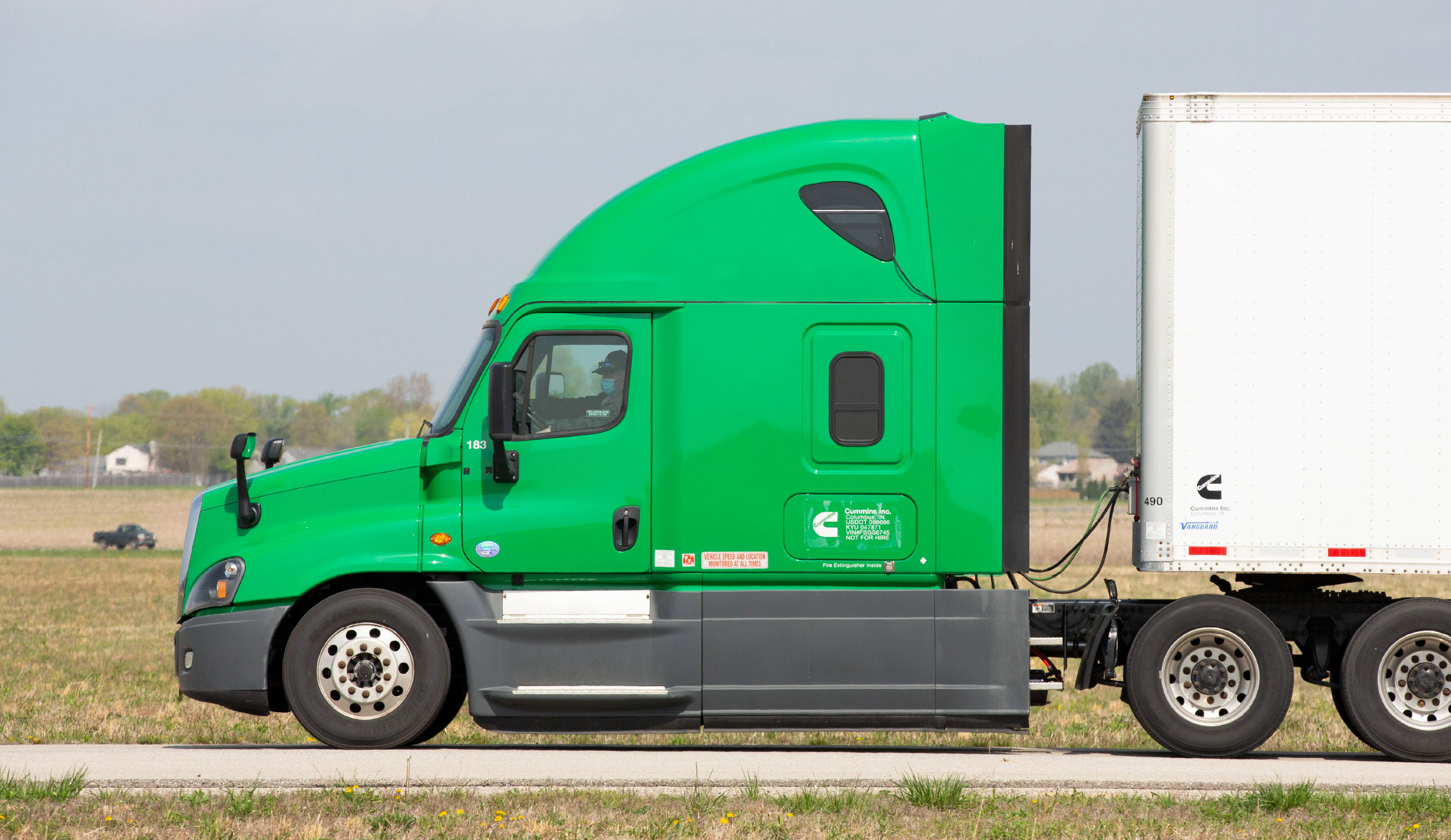
Tula has developed one of the essential technologies
for reaching fuel efficiency mandates
Click to learn more about Tula and our dedication to a cleaner Earth
Hybrid++
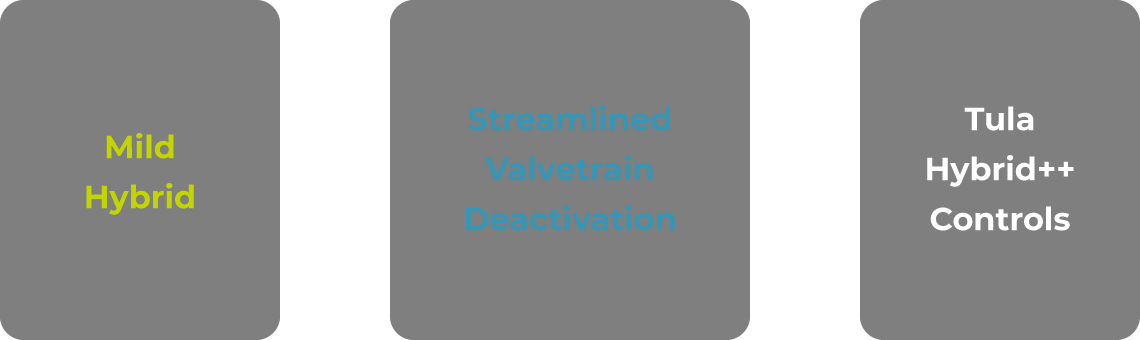
How Hybrid++ works
HYBRID++ is a simplified, patented all-cylinder deactivation controls technology, that is applicable to P0 or P1 Mild Hybrid Vehicles to achieve synergistic fuel efficiency gains and significant toxic emissions reductions.
HYBRID++™ in real world situations
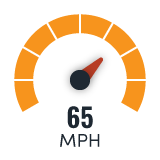
All cylinders fire during highway merging and the hybrid motor provides torque assist.
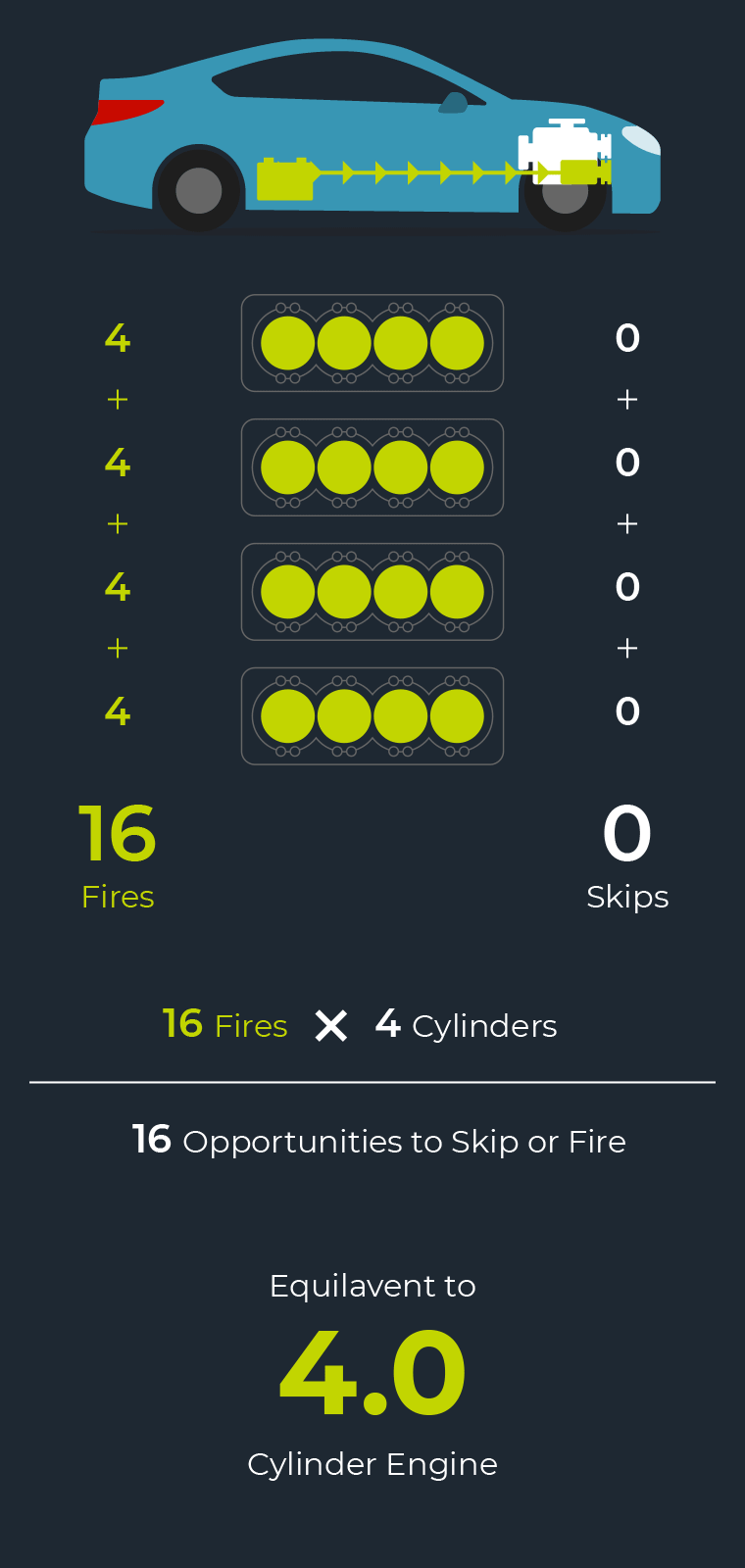
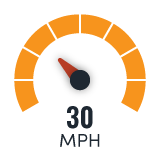
During low-speed cruise, the electric motor can propel the vehicle with all cylinders deactivated
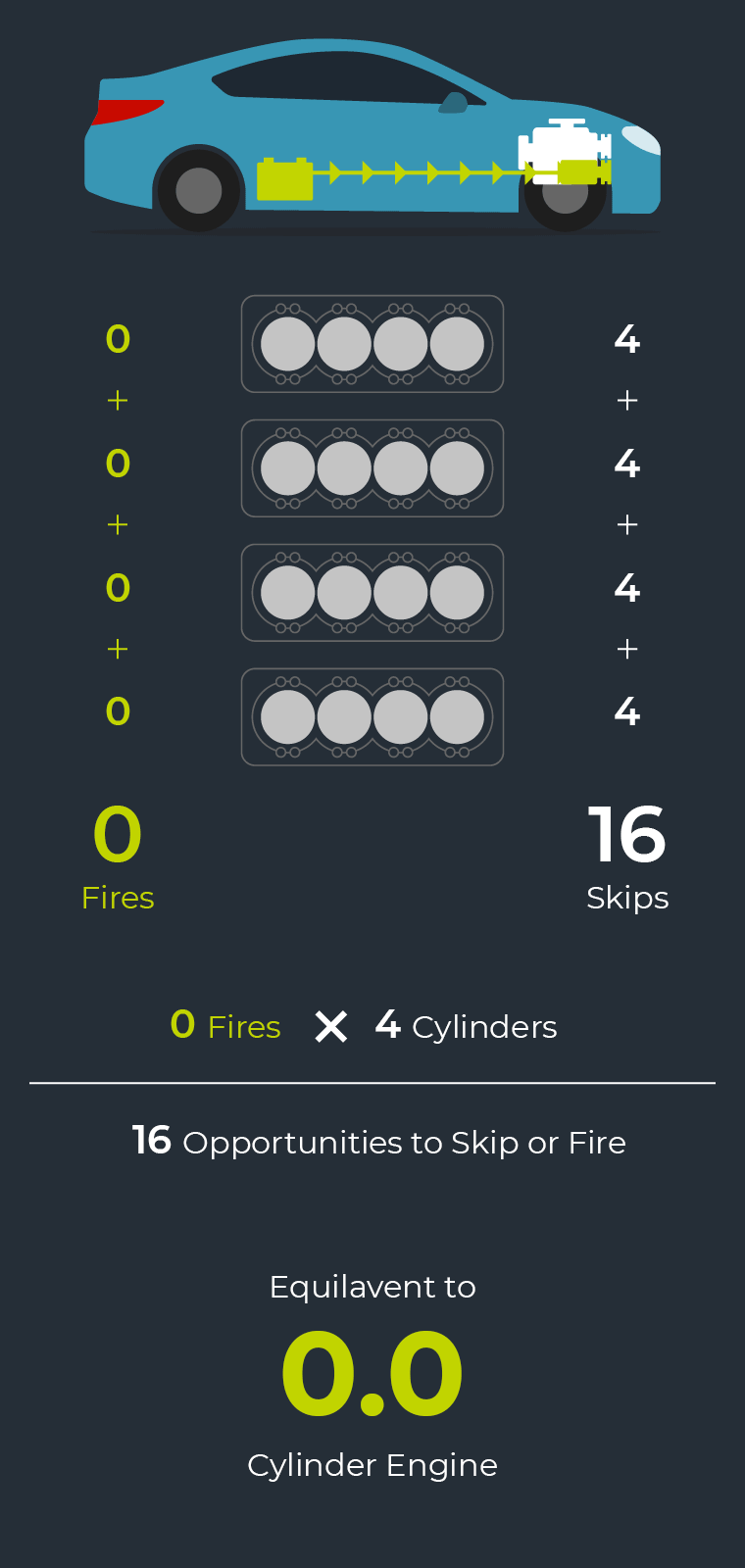
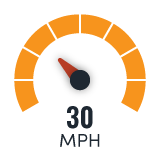
Lifting off the accelerator pedal causes all cylinders to deactivate and enables more recuperation. No air pumped into the exhaust.
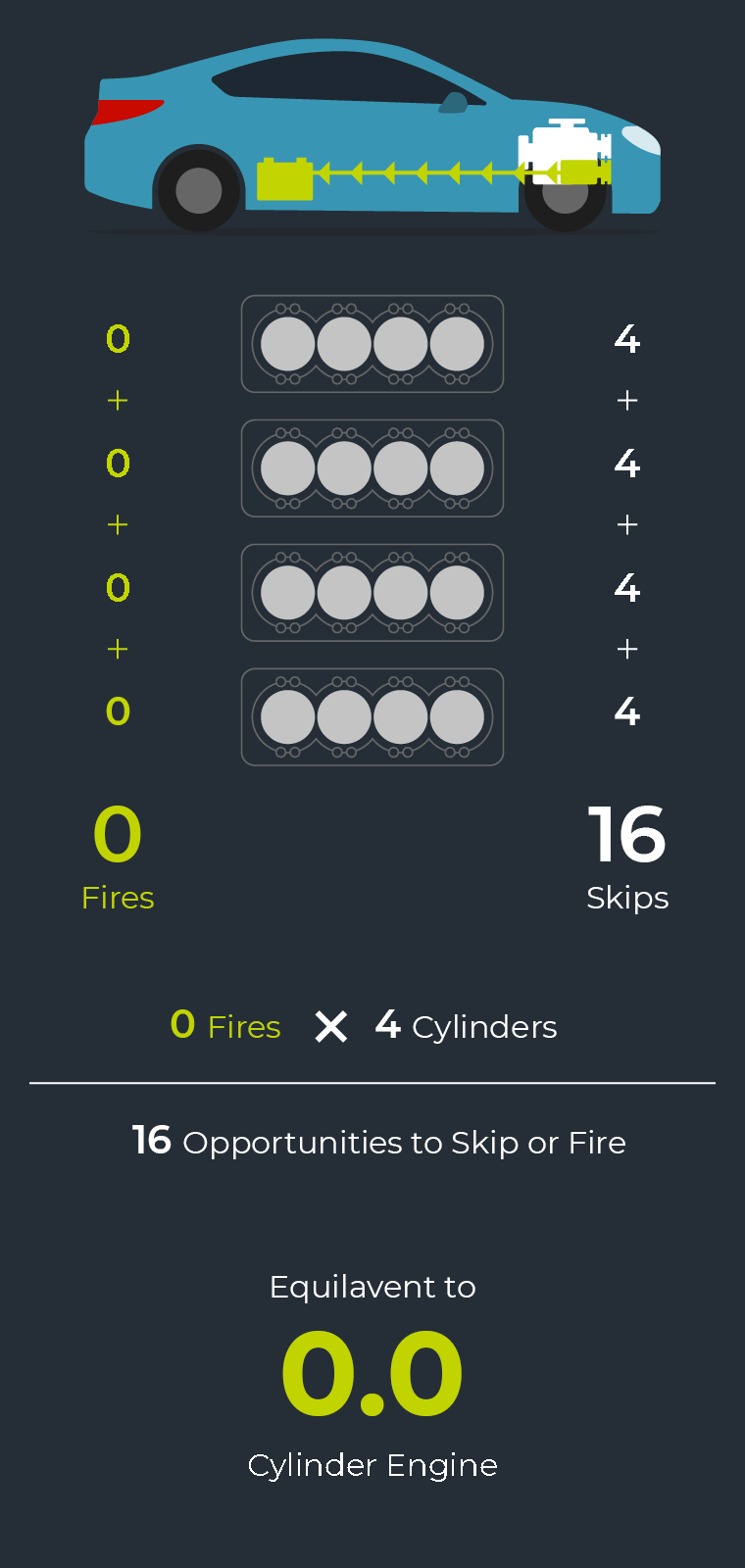
Hybrid++ eliminates pumping losses during coast and overrun conditions. Because air doesn’t get pumped into the exhaust during deactivation, Hybrid++ also significantly reduces the harmful emissions that otherwise come from purging the catalyst
CO2 reduction
Tula’s research findings on Dynamic Skip Fire
for Hybrid Powertrains
Click to learn more about Tula and our dedication to a cleaner Earth
DSF and 48V mild-hybrid synergies enable better fuel economy at lower cost
How eDSF works
eDSF synergystically combines cylinder deactivation with vehicle electrification to increase the operating range of DSF. By countering engine torque with motor torque at appropriate fires and skips, eDSF enables smoother operation and expansion of the DSF fly zone.
eDSF™ in real world situations
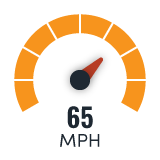
During highway cruising, the motor torque supplements the engine enabling it to fire on fewer cylinders
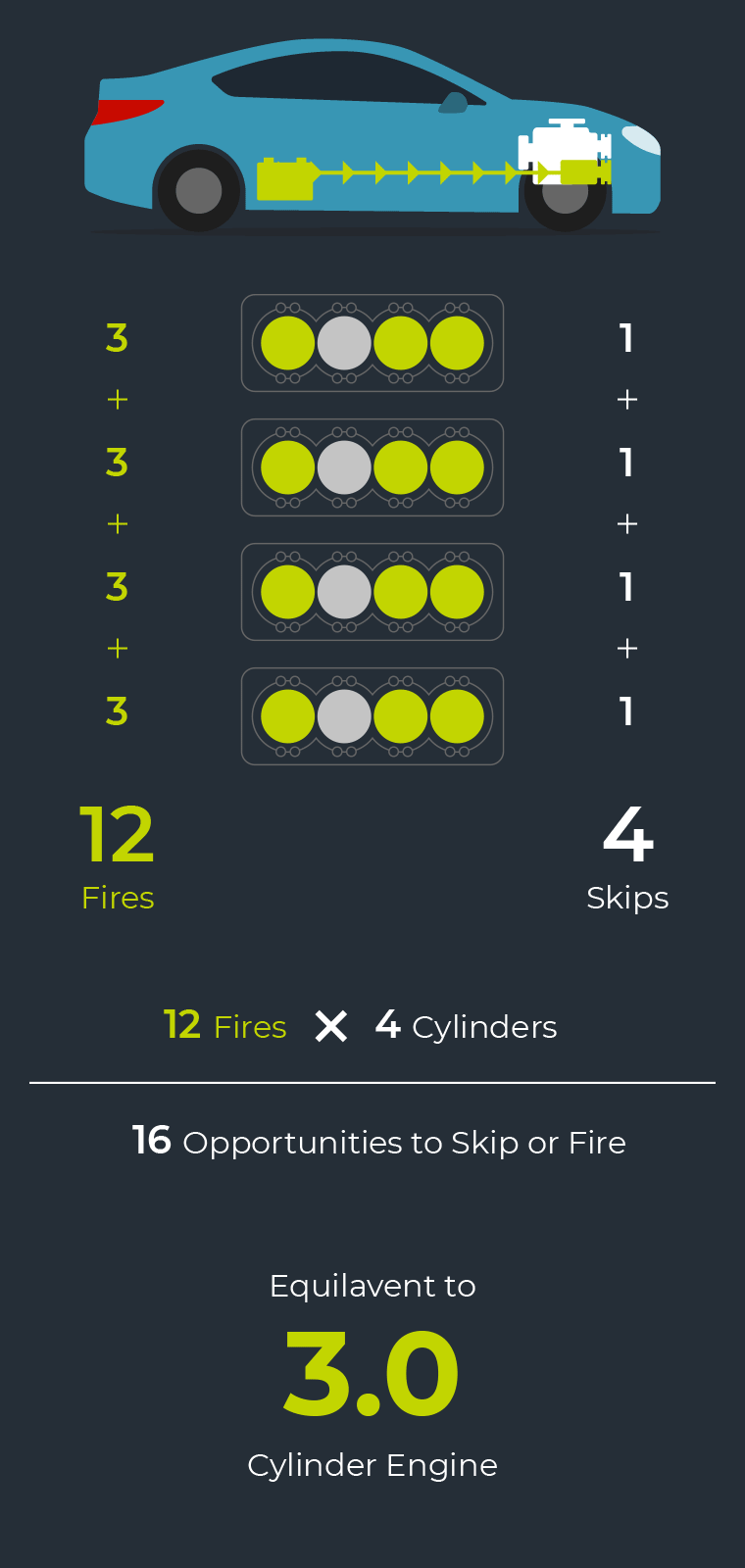
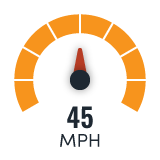
At low to medium loads, the expanded operating range due to torque smoothing and torque assist enables smooth and efficient eDSF operation.
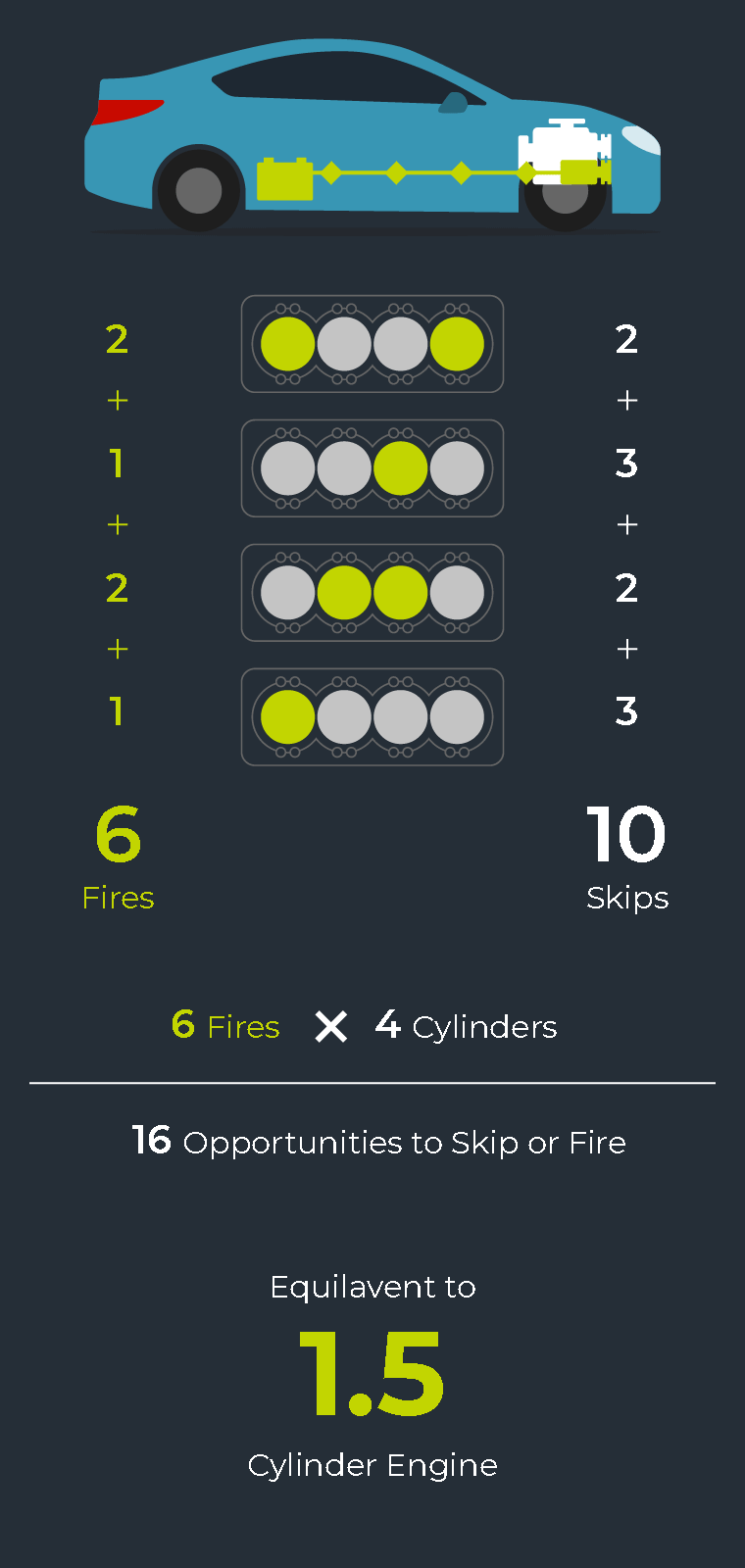
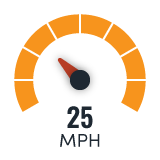
Enhanced Energy Recovery: eDSF shuts off all cylinders (called DCCO for Deceleration Cut Off) allowing hybrid systems to fully capture kinetic energy through regeneration without engine braking loss.
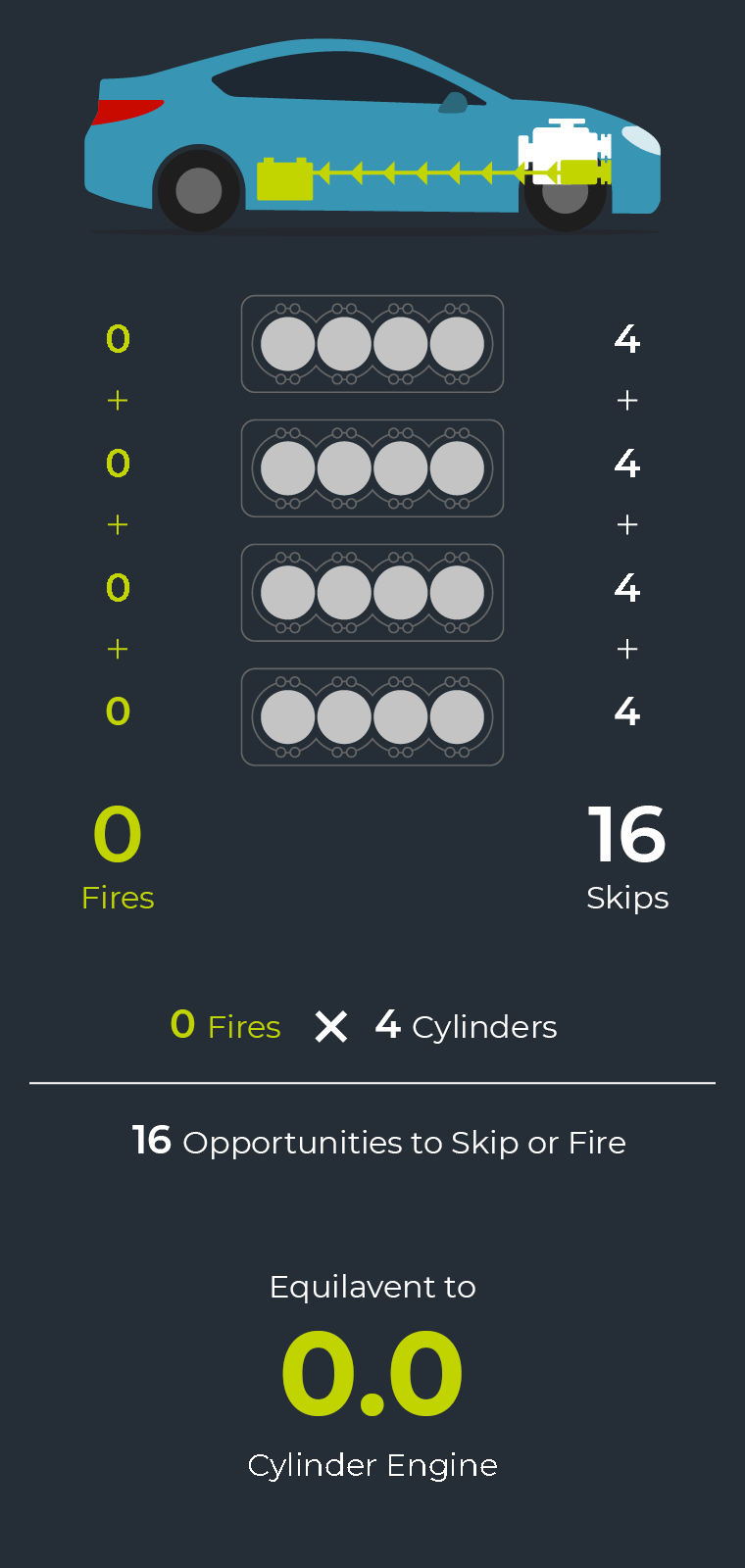
Electrification enables smoother torque
eDSF uses the existing hybrid motor to smooth torque pulses of skip fire operation
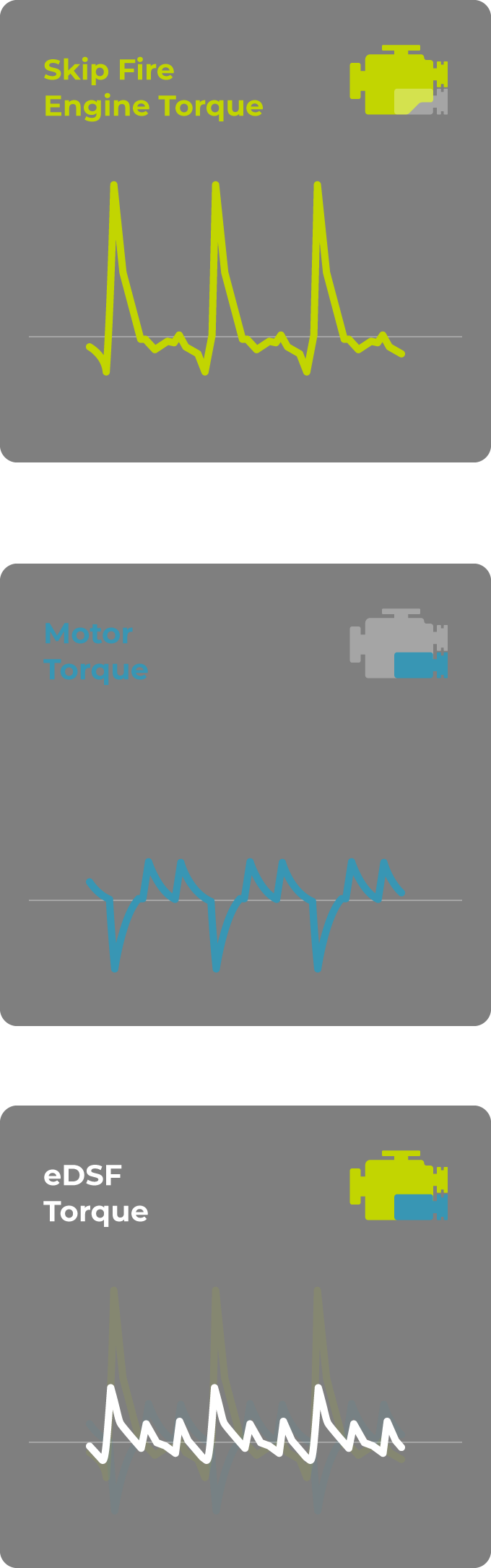
DSF operating range is increased
Electric motor torque smoothing and torque assist extend the range of useful firing densities.
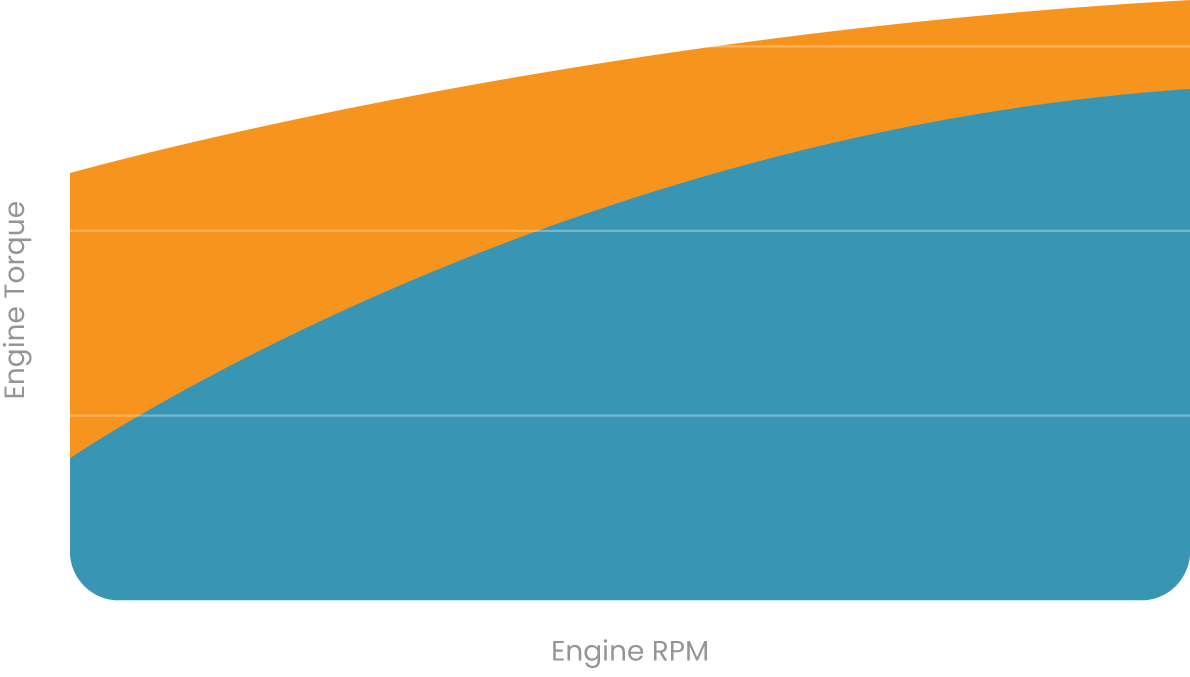
The combination of torque assist into DSF, increased regeneration and torque smoothing enables eDSF to deliver gains beyond what DSF and mild-hybrid could individually provide. eDSF is truly a whole that is greater than the sum of its parts.
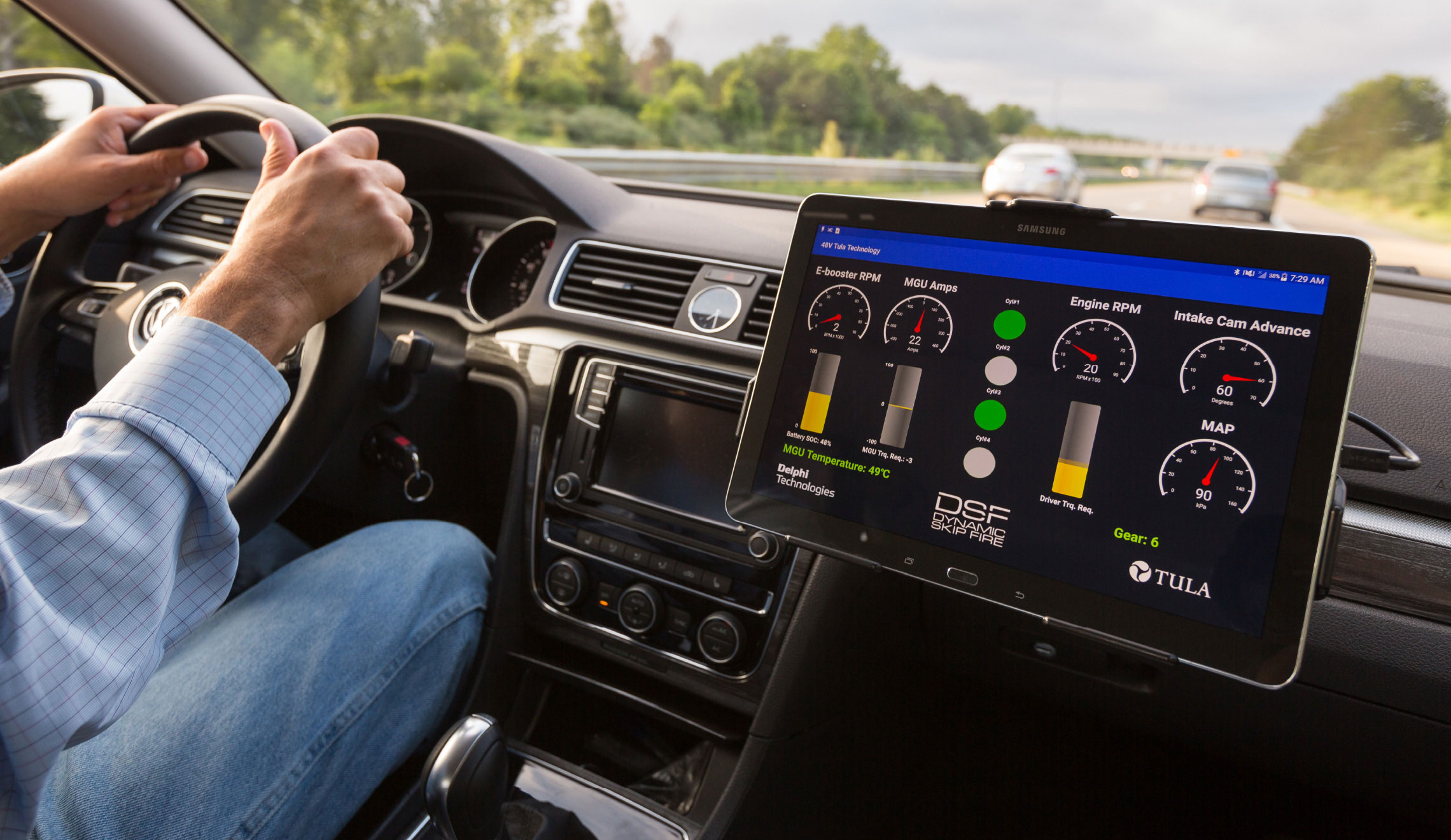
Advanced Technologies
DSF works synergistically with multiple advanced engine and vehicle technologies such as Miller-cycle and Atkinson-cycle engines, compressed natural gas and other alternative fuels as well as connected and autonomous vehicles.
Advanced Combustion
Miller-cycle engines hold fuel economy promise, but on a stand-alone basis are limited by efficiency-performance trade-offs
DSF® works synergistically with this advanced engine combustion strategy to strengthen its advantages while addressing its challenges.
mDSF more than doubles the fuel efficiency improvement of Miller-cycle engines on a stand-alone basis, while lowering the cost per percent improvement.
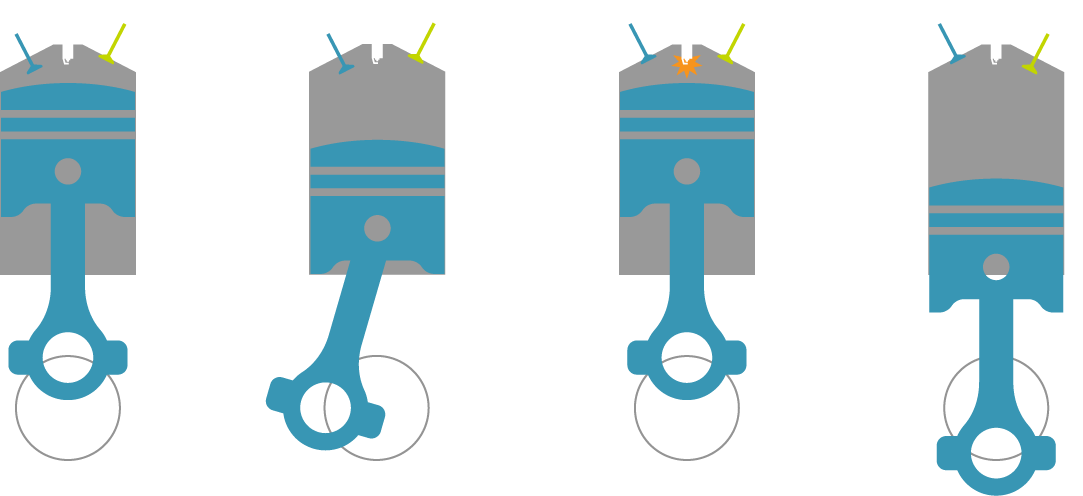
How mDSF works
mDSF couples DSF with Miller-cycle engines to further increase each cylinder’s firing options with high-fire, low-fire and skip to match torque demand always at optimum efficiency without sacrificing drivability.
Dynamic charge management using mDSF has synergistic benefits beyond those provided by DSF and Miller-cycle engines individually.
CO2 reduction
toxic emissions
noise, vibration, harshness
Tula’s research and development publications on
advanced applications using DSF®
Click to learn more about Tula and our dedication to a cleaner Earth
Only a few years ago, self-driving cars were considered science-fiction
Today, autonomous cars are a rapidly evolving technology. These vehicles are designed to be wirelessly connected to each other and the cloud infrastructure, providing the engine controller actionable information about vehicle position, traffic, terrain, obstacles, traffic light changes, and more.
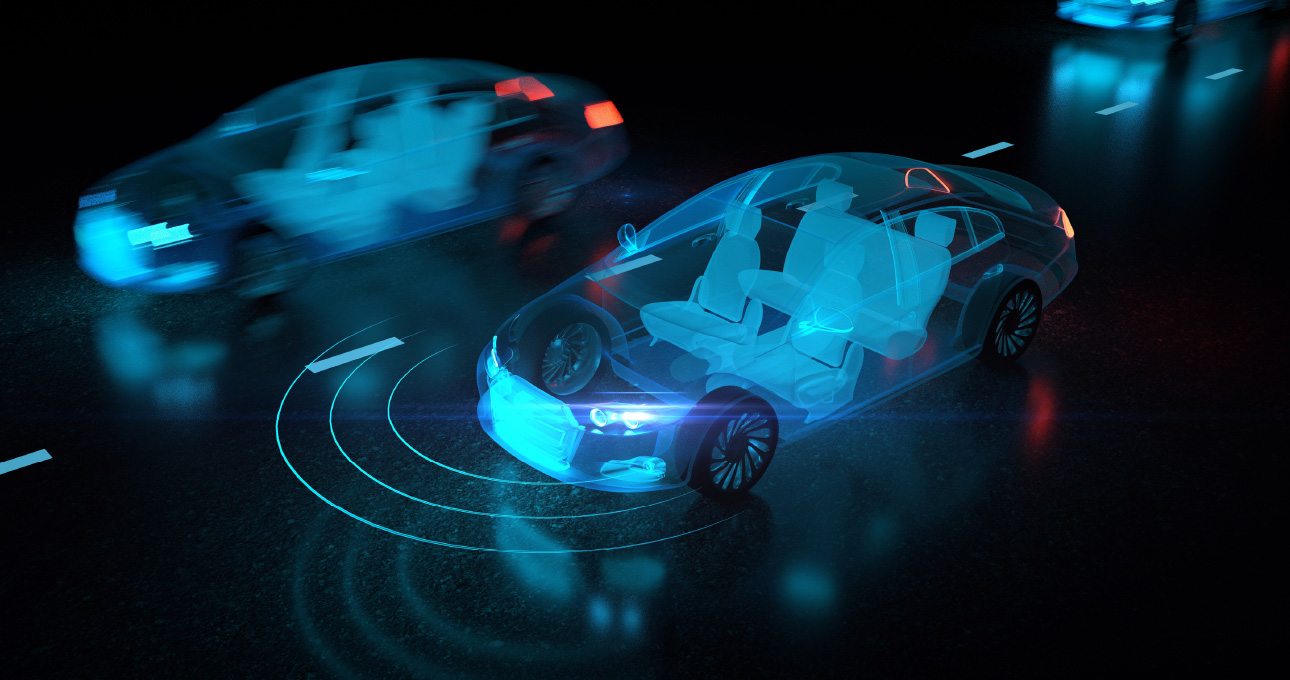
How DSF works in tandem with Autonomous
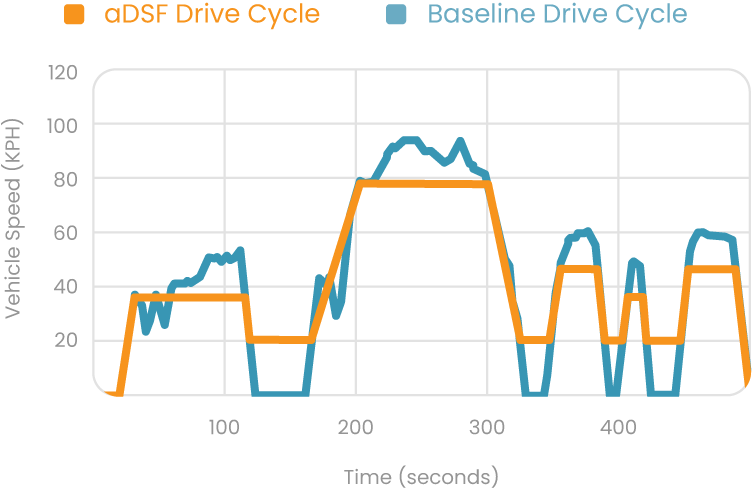
The blue curve in the graph illustrates a typical drive cycle of rapid accelerations, slowdowns, braking and stops. The orange curve is for an autonomous vehicle that anticipates traffic signals and other obstacles.
aDSF delivers significant fuel efficiency gains by not only optimizing for the autonomous drive cycle but also optimizing the drive cycle itself. Moreover, autonomous cars can be fully unoccupied at various times, unconstrained by noise, vibration and harshness issues, leading to further aDSF efficiency benefits.
CO2 reduction
Drive Cycle
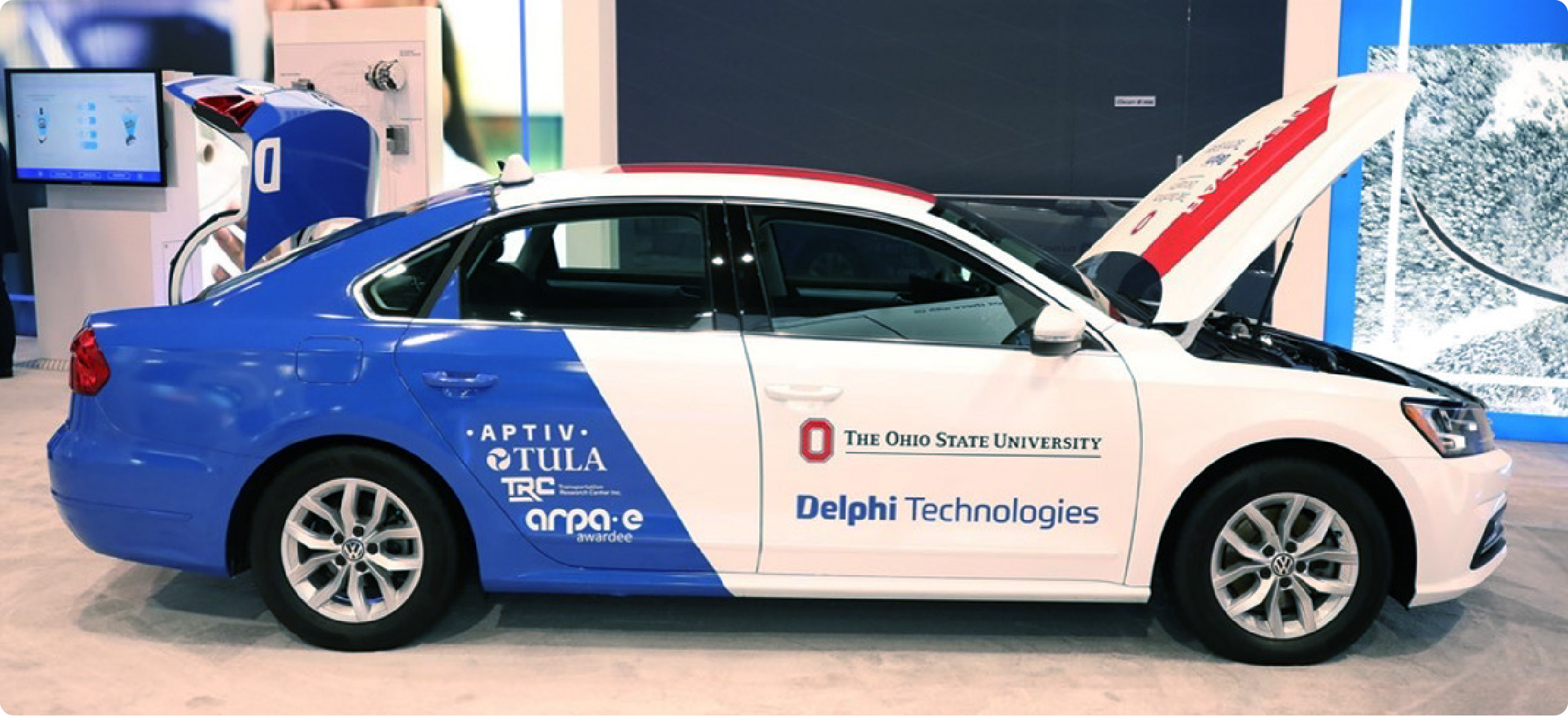
Tula’s research and development publications on
advanced applications using Autonomous
Click to learn more about Tula and our dedication to a cleaner Earth
Alternative Fuels
Tula’s DSF control strategies can be applied to engines designed to use alternative fuels, both improving powertrain efficiency and reducing harmful emissions
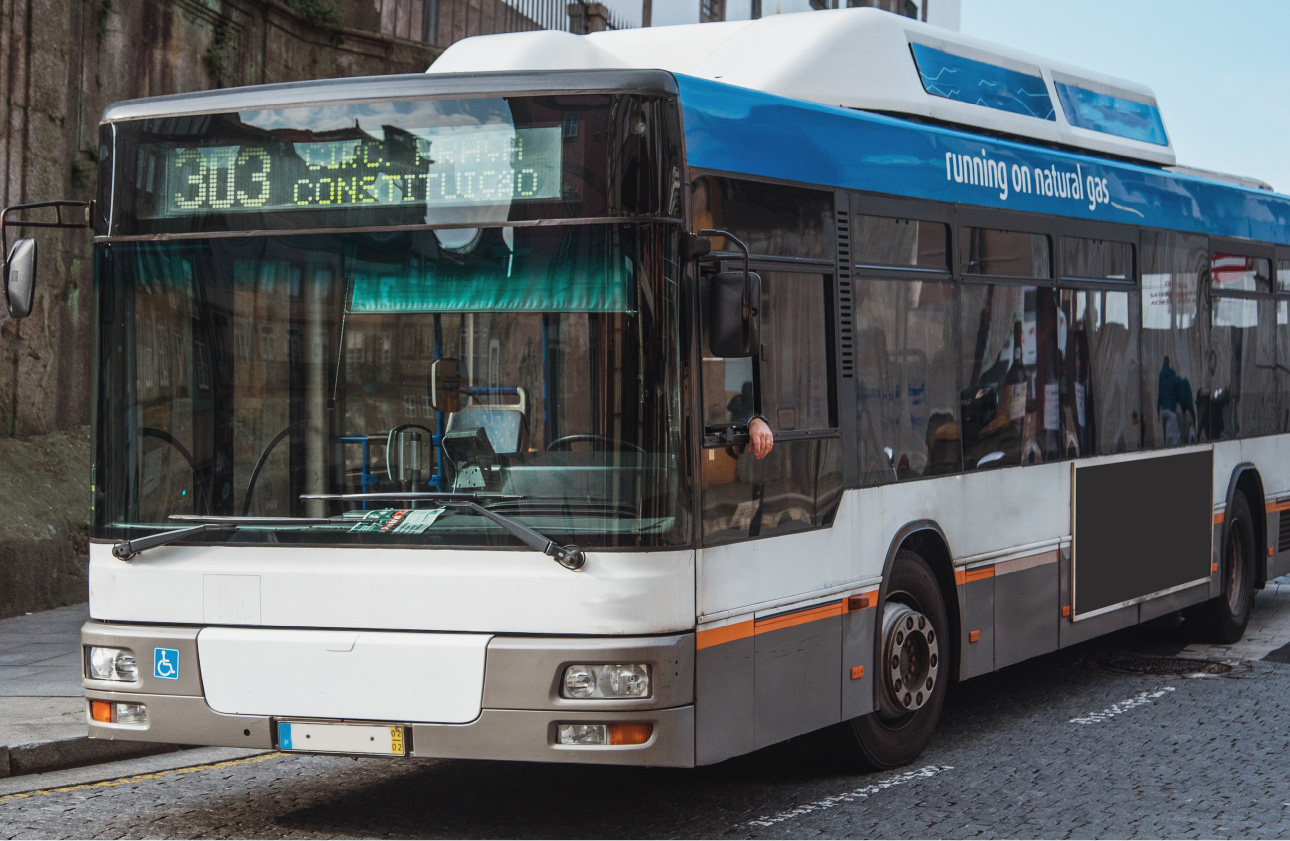
According to U.S. Energy Information Administration, alternative fuels are projected to grow much faster than petroleum in the transportation sector. With DSF for gasoline, diesel, and alternative fuels, plus DMD technology for electric vehicles, Tula is poised to further improve emission and cost benefits for decades into the future.
Transportation sector consumption of minor petroleum and alternative fuels (AEO2020 Reference case) quadrillion British thermal units
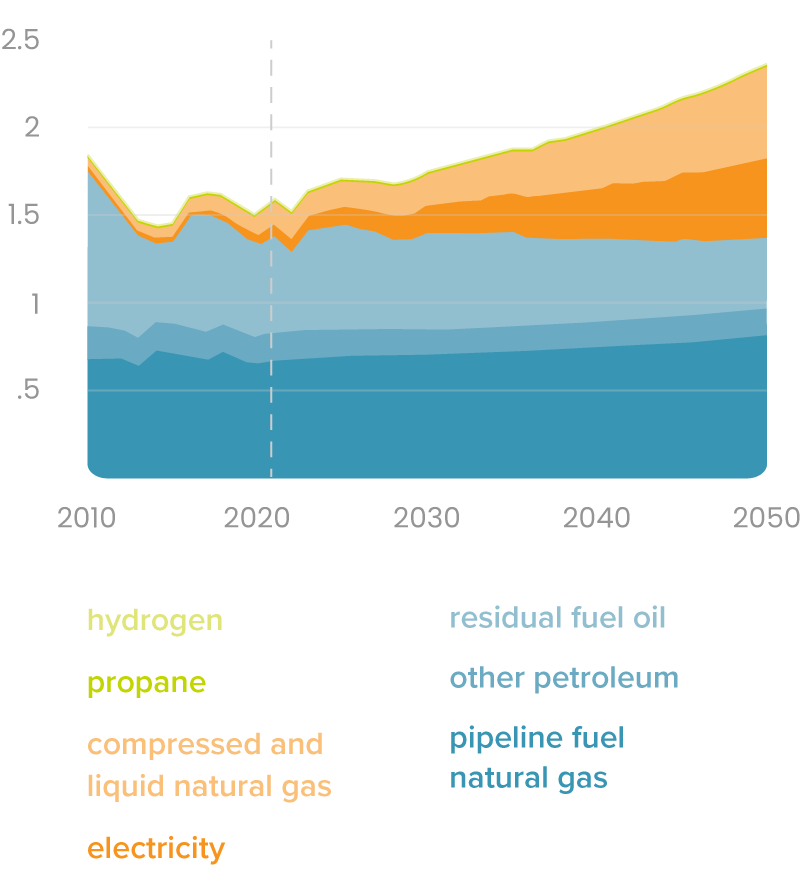